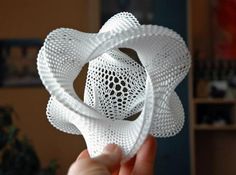
ساخت افزایشی بر مبنای ذوب پودری را بشناسیم
*فرشید ریخته گر
مواد اولیه می تواند به شکل های پودر و سیم مورد استفاده قرار گیرد و انرژی حرارتی مورد نیاز ممکن است از طریق لیزر یا پرتو الکترونی تامین شود. بر این اساس تکنولوژی ساخت افزایشی برای مواد فلزی به دو گروه اصلی روش های ذوب بستر پودری (PBF) و سیستم های تغذیه پودری مانند رسوب مستقیم فلز (DMD) دسته بندی می شوند. در نوع اول، انرژی حرارتی به صورت انتخابی مناطقی از بستر پودری را ذوب می کند که از جمله روش های اصلی این گروه می توان به تفجوشی یا ذوب انتخابی با لیزر (SLS/SLM) و ذوب با پرتو الکترونی (EBM) اشاره نمود. در نوع دوم، ذوب مواد اولیه (به شکل پودر یا سیم) از طریق منبع حرارتی و همزمان با رسوب آنها روی سطح انجام می پذیرد و با توجه به نوع دستگاه و ویژگی های آن، روش های مختلفی مانند DMD، LENZ و EBFFF در این گروه قرار می گیرند.
ساخت افزایشی بر مبنای ذوب بستر پودری
بستر پودری در یک خلا نسبی یا اتمسفر خنثی قرار دارد تا از فلز مذاب به طور کامل حفاظت شود. منبع انرژی (لیزر یا پرتو الکترونی) برای روبش هر لایه پودر پخش شده روی بستر و ذوب انتخابی ذرات پودر مطابق با نقشه مدل قطعه، مورد استفاده قرار می گیرد. زمانی که یک لایه به طور کامل روبش شد، پیستون محفظه ساخت به اندازه ضخامت یک لایه پایین رفته و پودر جدید مجددا توسط غلتک روی سطح پخش می شود. این سیکل به صورت لایه به لایه ادامه پیدا می کند تا کل قطعه به صورت کامل شکل بگیرد. حاصل این فرآیند یک جعبه به صورت کیک پودری بوده که از ماشین خارج می شود و قطعات ساخته شده داخل آن قابل رویت نیستند.
در برخی موارد به ویژه برای قطعات پیچیده با سطوح منحنی معلق، نیاز به استفاده از ساختارهای مشبک پشتیبان جهت جلوگیری از اعوجاج قطعه و توزیع یکنواخت حرارت در حوضچه مذاب وجود دارد. این سازه های پشتیبان معمولا طی عملیات نهایی پس از تولید، به صورت مکانیکی حذف می شوند. پس از این مرحله، قطعات ممکن است بسته به نیاز تحت عملیات نهایی دیگری مانند ساچمه زنی، صیقل کاری، ماشینکاری و یا عملیات حرارتی قرار گیرند. همچنین به منظور افزایش چگالی، برخی قطعات نیاز به عملیات پرس ایزواستاتیک گرم (HIP) دارند.
سیستم های لیزری
سیستم فرآیند SLS اولین بار در سال 1986 توسط Carl Deckard ساخته شد و تجاری سازی آن در سال 1992 توسط DTM Corporation انجام شد. اولین ماشین تفجوشی لیزری تجاری نیز به وسیله شرکت EOS با نام EOSINT M250 در سال 1995 در کشور آلمان روانه بازار شد. روش SLM که حالت پیشرفته SLS به حساب می آید و در آن ذوب کامل بستر پودری در هر لایه با استفاده از یک یا چند لیزر اتفاق می افتد، در سال 1999 توسط Fockele و Schwarze با همکاری موسسه تکنولوژی لیزر فرانهوفر آلمان معرفی گردید و توسط شرکت MCP HEK Gmbh (هم اکنون SLM Solutions) با ماشین MCP Realizer250 به صورت تجاری وارد بازار پرینترهای سه بعدی شد.
اغلب این سیستم ها از یک لیزر فیبر با توان 1000-200 وات برای ذوب انتخابی بستر پودر استفاده می کنند. توان لیزر، سرعت روبش، فاصله بین مسیرهای حرکت لیزر و ضخامت لایه های پودر از متغیرهای اساسی در فرآیندهای PBF به شمار می آیند. بسته به نوع ماده، ضخامت هر لایه بین 100-20 میکرومتر انتخاب می شود. همه فرآیندهای فوق قادر به تولید قطعاتی کاملا چگال از جنس آلیاژهای مختلف مانند تیتانیم، اینکونل، کبالت کروم، آلومینیم، فولادهای زنگ نزن و فولادهای ابزار هستند.
بیشتر ماشین آلات با تکنولوژی PBF و سیستم لیزری، نرخ ساخت پایینی بین cm3/h 20-5 دارند و حداکثر اندازه قطعه قابل تولید با توجه به محفظه ساخت آنها mm3 325×250×250 می باشد که محدودیت هایی در انتخاب اندازه محصولات و هزینه های تولید ایجاد می کند. به این ترتیب در سال های اخیر، سازندگان ماشین و مراکز تحقیقاتی، همواره به فکر افزایش ظرفیت های این تکنولوژی با درنظرگیری افزایش حجم ساخت و نرخ تولید قطعات بوده اند. به عنوان نمونه، شرکت SLM Solutions در سال 2012 پرینتر SLM500 HL را با دو ست منبع لیزر معرفی نمود که نرخ ساخت cm3/h 35 و ظرفیت mm3 300×350×500 را ارائه می کند.
استفاده از دو ست لیزر که هر کدام دارای دو لیزر با توان های 400 و 1000 وات هستند، به این مفهوم است که در این ماشین، همزمان 4 لیزر روی بستر پودری حرکت کرده و سرعت ساخت هر لایه را افزایش می دهند. شرکت EOS نیز در سال 2013، از ماشین EOSINT M400 رونمایی نمود که جهت افزایش سرعت ساخت در آن از لیزر فیبر 1 کیلووات و محفظه ساخت mm3 400×400×400 استفاده شده است. همچنین موسسه تکنولوژی لیزر فرانهوفر آلمان و شرکت Concept Laser، بزرگترین سیستم AM برای فلزات را با حجم محفظه ساخت mm3 500×400×630 و نرخ تولید قطعه تا cm3/h 100 با نام Xline 1000R به بازار عرضه کرده اند.
ذوب با پرتو الکترونی
روش EBM یکی دیگر از روش های ذوب بستر پودری AM است که در آن ذوب ذرات پودر با استفاده از پرتو الکترونی در اتمسفر خلا و به صورت انتخابی انجام می پذیرد. این روش توسط شرکت سوئدی Aracm در سال 1997 معرفی شد. در روش EBM، با اعمال اختلاف پتانسیل، فیلامان تنگستنی داغ شده و پرتو الکترونی با سرعت بالا ساطع می کند که در ادامه، توسط میدان های مغناطیسی و کویل های روبش، به سمت سطح بستر پودری هدایت می شود. زمانی که الکترون ها با سرعت بالا به سطح برخورد می کنند، انرژی جنبشی آنها به حرارتی تبدیل شده و منجر به ذوب ذرات پودر فلز می گردد. هر لایه دوبار در مراحل پیش گرمایش و ذوب، تحت روبش قرار می گیرد. در مرحله پیش گرمایش پرتو الکترونی به صورت واگرا با سرعت زیاد برای آماده سازی بستر پودری به کار می رود و سپس در مرحله ساخت قطعه، پرتو متمرکز با سرعت کمتر برای روبش و ذوب هر لایه اعمال می شود.
کل فرآیند EBM در خلا بالا به میزان mbar 5-10-4-10 انجام می شود. استفاده از گاز هلیم حین ساخت، فشار خلا مورد نیاز را کاهش می دهد و همچنین، منجر به خنک سازی قطعه و پایداری پرتو الکترونی می گردد. در مواردی برای افزایش سرعت تولید، پرتو الکترونی به چندین پرتو منفرد تبدیل می شود که هر یک می تواند برای حرارت دهی، تفجوشی و یا ذوب بستر پودری در هر لایه مورد استفاده قرار گیرد. سیستم EBM شرکت Arcam، از پرتو الکترونی توان بالا (W 3000) استفاده می کند و طیف گسترده ای از آلیاژهای فلزی با این روش قابل فرآوری می باشند. توان پرتو الکترونی، شدت جریان، قطر پرتو متمرکز، دمای پیش گرم بستر پودر و ضخامت هر لایه از متغیرهای مهم در روش EBM می باشند. ضخامت هر لایه در این روش بین mµ200-50 قرار دارد.
* عضو کمیته مشاوران دومین رویداد جامع ساخت افزایشی
Send to friends